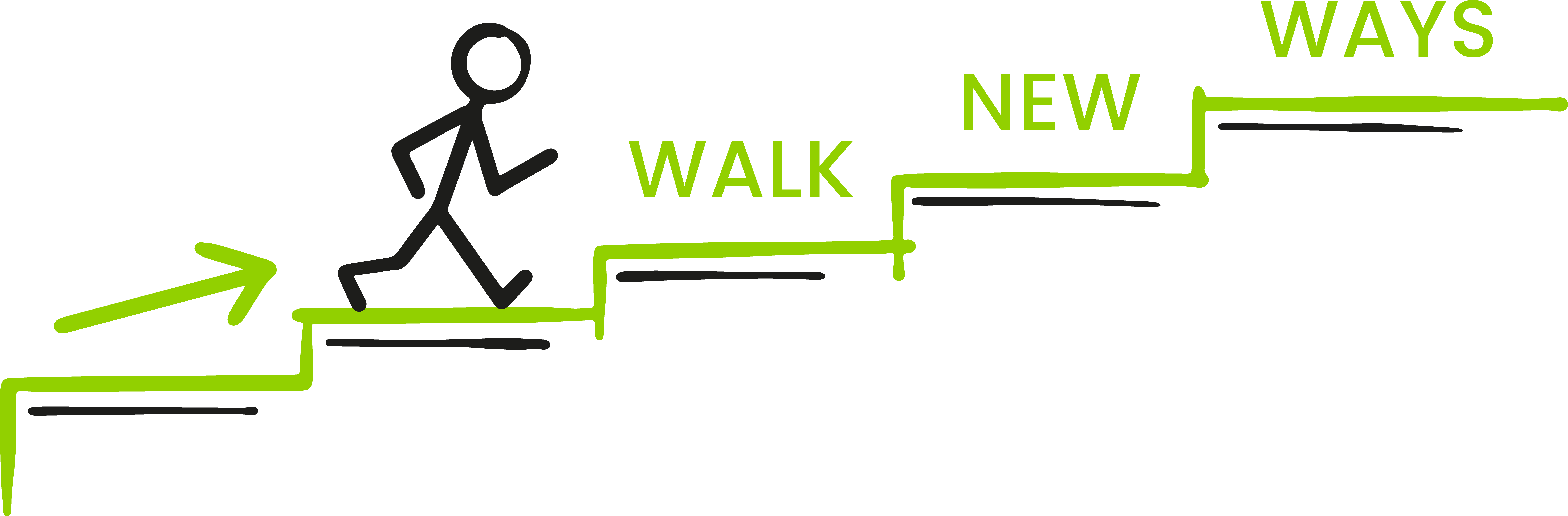
What is 3D printing and how does it work?
The colloquial term 3D printing is now known as additive manufacturing and is the opposite of subtractive processes. In subtractive processes, material is removed from a compact block of material using milling, turning or drilling to form a component. Additive manufacturing, in contrast, is a material-applying process in which the component is built up layer by layer, free of geometric constraints.
What are the advantages of 3D printing?
3D printing offers advantages over conventional manufacturing processes in several respects:
- Low expenditure of time and materials
- Shape and function optimization
- Customized products
- Geometrically intricate and complex components
- Without additional tool
- Internal complex structures such as channels, thin-walled or loose parts
Especially in the field of small series and prototype production, we see 3D printing as the ideal process here.
This also works with ceramics?
Ceramic components can also be produced using 3D printing. Stereolithographic 3D printing (STL for short) was the first technology to produce ceramic components that were used in industry as high-performance ceramics. STL technology can be used to produce thin-walled, highly complex and virtually form-free ceramic components. New and revolutionary are the processes we use for the industrial production of thin- to thick-walled and complex ceramic components. We rely on the Laser Induced Slip Casting process (LIS for short) and the Layer-by-Layer Slip Deposition process (LSD for short). The addition of these two printing processes pushes the boundaries in the production of ceramic components.
New and revolutionary are the processes we use for the industrial production of thin- to thick-walled and complex ceramic components. We rely on the Laser Induced Slip Casting process (LIS for short) and the Layer-by-Layer Slip Deposition process (LSD for short). The addition of these two printing processes pushes the boundaries in the production of ceramic components.
Why do we need 3D printing in ceramics?
The manufacturing processes or methods in ceramics have not changed in the last hundred years. There are basically only four industrial molding processes, pressing from powder or granules, extrusion from plastic masses, and slip and injection molding from ceramic suspensions. All processes require an adapted molding tool for each new component. These are very expensive and in most cases only economical for quantities of more than 10,000 components. This makes them unsuitable for the production of prototypes or small batches. Furthermore, the component complexity is limited with the conventional processes. Especially in todays world, the demand for component complexity and shape flexibility is increasing more and more because the associated products are expected to become smaller and lighter. As a result, the industry is in need of new molding processes. 3D printing is able to close this gap.
And what is the difference between LIS and LSD?
With both processes, dense, thick-walled ceramic components can be produced quickly and easily, regardless of the material and its particle sizes. This is made possible by processing water-based and virtually organic-free suspensions. Basically, LSD stands for higher resolution and detail accuracy. However, LIS is ideal for the rapid production of single medium-sized prototypes with high wall thickness.
Have a look at the technological differences of the processes in detail on the corresponding subpages: